Ultimate Guide to Aluminum Laser Cutting | Challenges & Pro Tips
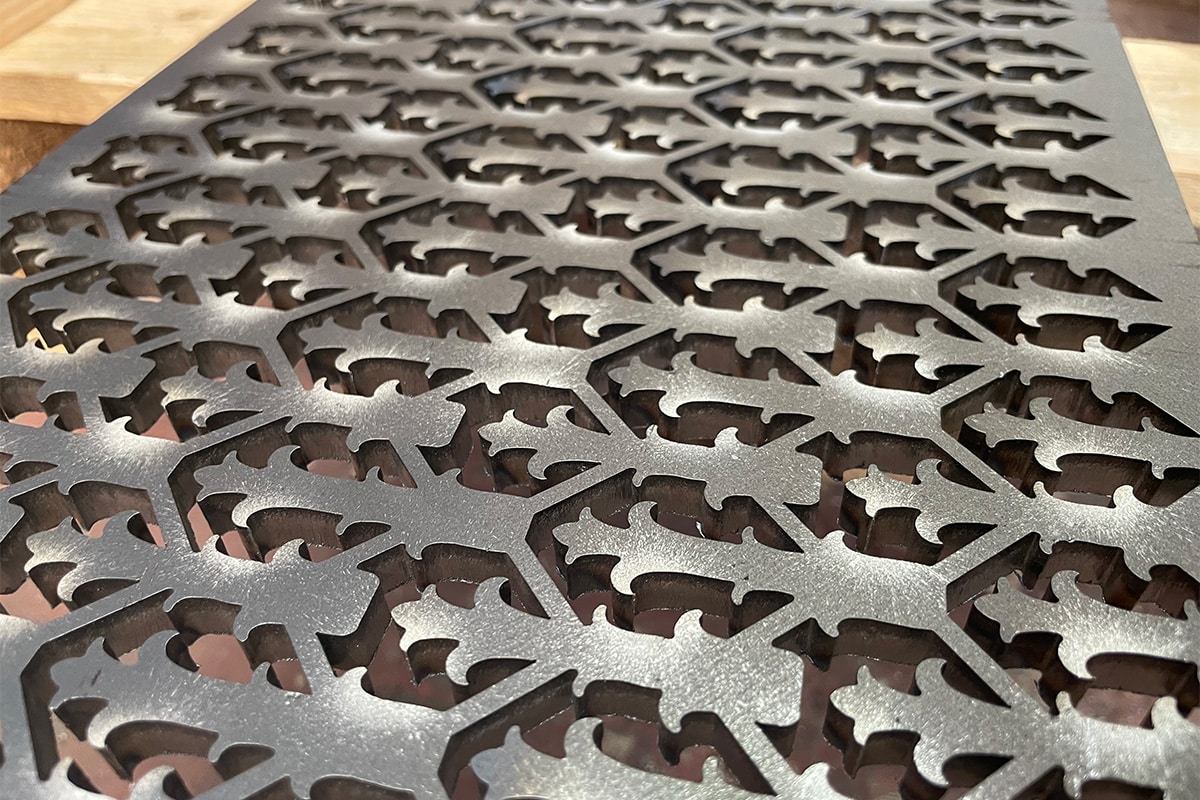
Aluminum laser cutting is undoubtedly one of the most challenging processes in the world of manufacturing. While it’s not impossible, it needs certain level of expertise and precision.
But why is aluminum so difficult to cut with a laser?
Well, it’s because of its unique properties. With high reflectivity, exceptional thermal conductivity, tricky molecular structure, aluminum doesn’t always play nicely with laser beams. These characteristics can make it hard to achieve a clean, smooth edge during the cutting process.
In this blog post, we’ll explore the properties that make aluminum a challenging material for laser processing. Additionally, we’ll share some expert tips to help make your lasing cutting successful and achieve flawless results. If you’re searching for professional assistance, United Metals Laser has you covered with advanced equipment and expert laser cutting service in Perth.
Why is Aluminum Laser Cutting So Popular?
Using a laser cutting machine for aluminum offers several advantages:
- Exceptional precision and accuracy for intricate designs.
- Faster speed compared to traditional cutting methods.
- Works for a variety of thicknesses and applications.
- More efficiency and cost-efficient.
Despite these benefits, laser and cutting aluminum comes with some challenges. Let’s explore them next.
Top 5 Challenges of Aluminum Laser Cutting
Cutting aluminum with a laser isn’t always easy. Its unique characteristics can create several obstacles. But with the right techniques, these challenges can be managed effectively. Here are the most common hurdles you may encounter when laser cutting aluminum:
1. High Reflectivity
Aluminum’s shiny surface makes it highly reflective, which is a major challenge for laser cutters.
When the laser beam hits the material, it tends to bounce back or scatter. This potentially damages the laser cutting machine. Materials like stainless steel also pose similar challenges. But aluminum’s high reflectivity makes it even harder to work with.
Some manufacturers try to coat the aluminum with a non-reflective substance to minimise the issue. But this solution is not foolproof. Once the coating is pierced and the aluminum begins to melt, its reflective surface is exposed again. This makes the process just as tricky.
2. Material Composition Matters
Not all aluminum grades are created equal. Pure aluminum grades, like AW 1050, mostly have fewer alloying elements. This makes them more reflective and harder to cut.
On the other hand, aluminum alloys contain elements that can help reduce the reflective effect which makes them slightly easier to work with during laser cutting process.
3. Burr Formation
A common issue with aluminum laser cutting is the formation of burrs along the edges. Burrs not only affect the material’s appearance but can also need additional processing to remove them.
- Some manufacturers use mechanical methods to remove burrs after cutting.
- Others focus on precise machine setups to avoid burr formation altogether. This one is mostly the preferred solution as it eliminates extra costs for the client.
4. Molecular Structure Challenges
Aluminum’s soft molecular structure causes another layer of complexity. Unlike materials with solid and stable molecular structures, aluminum’s softer nature makes it harder for the laser beam to pierce through and create clean, precise cuts. This can result in jagged edges and uneven finishes.
5. Thermal Conductivity
One of the biggest hurdles in laser cutting aluminium is its excellent heat conductivity.
Aluminum quickly absorbs the heat generated during the cutting process. This can make it difficult to maintain the temperature needed for smooth cutting. This heat dissipation can also lead to uneven cuts and other processing difficulties.
Expert Tips for Laser Cutting Aluminium | Overcoming the Challenges
Wondering how to cut aluminum sheets the right way? Let’s explore some expert tips to overcome the challenges of aluminum laser cutting. Despite being reflective, soft, and thermally conductive, aluminum can be successfully cut using CO2 or fiber lasers.
Here’s how to do it effectively.
1. Consider Fiber Lasers vs. CO2 Lasers for Aluminum Cutting
When it comes to laser cutting aluminum, the choice between fiber lasers and CO2 lasers makes a huge difference. Each laser has its own strengths. But fiber lasers stand out for handling reflective materials like aluminum more effectively.
- Fiber lasers: Designed specifically for cutting reflective surfaces. They use a solid-state setup that eliminates the risk of damage from bouncing laser beams.
- CO2 lasers: These rely on mirrors to direct the beam, making them more prone to issues with reflection. This can lead to reduced performance and potential damage to the equipment.
Here’s a quick comparison between fiber and CO2 laser to help you decide:
Feature |
Fiber Laser |
CO2 Laser |
Cutting Speed |
Faster |
Slower |
Power Efficiency |
High |
Lower |
Maintenance Needs |
Low |
High |
Performance on Aluminum |
Excellent |
Moderate |
Operating Costs |
Low |
High |
For both flat and tube aluminum cutting, fiber lasers are the superior option.
They offer better precision, higher efficiency, and are far more reliable for dealing with aluminum’s reflective properties. If you’re looking for smooth, accurate results, a fiber laser is the way to go.
2. Use the Right Metal Cutting Head
A metal cutting head is a must when working with aluminum laser cutting, especially with a CO2 laser. This specialised head is designed to handle metals effectively. This metal cutting head features:
- A protective window to prevent spark reflections that can damage the laser cutting machine.
- Adjustable focus knob to make sure the beam is at the optimal distance for clean cuts.
These features allow precise adjustments, eliminates guesswork, and enhances the cutting process for smoother results.
3. Create Clean-Cut Aluminum Edges
To achieve smooth, burr-free edges, focus on the following two things:
- High pressure: Helps cut through the material fast and efficiently.
- Gas assist: Removes any molten material quickly, preventing rough edges.
The faster you cut, the smoother the edges. High-wattage lasers are particularly effective. As they allow for increased speed and precision.
Using a fiber laser with higher wattage enables faster cutting speeds, resulting in cleaner kerf lines. Unlike routers or CNC cutters, laser cutting is a non-contact process. The only thing interacting with the aluminum is light, which eliminates the need for clamping and prevents damage to the material. This makes aluminum laser cutting both efficient and gentle.
4. Choose the Right Aluminum Grade
Different aluminum grades behave differently during laser processing. For example:
- Grades with more alloying elements (like aerospace and marine-grade alloys) are easier to cut.
- Pure aluminum grades, like AW 1050, are more reflective and harder to work with.
So, selecting the right grade for your project can save time and improve results.
5. Manage Focus and Reflection
Aluminum’s reflective nature is a major challenge. To handle it effectively:
- Adjust focusing distances: Keep the focus point toward the far side of the material to reduce dross.
- Prevent reflections: Use a laser cutter designed for reflective surfaces, such as fiber lasers.
6. Understand Thickness Limitations
For cutting with a laser, aluminum thickness plays a big role in determining the best approach:
- Up to 8mm: Laser cutting is the best option that provides speed and precision.
- Beyond 8mm: Consider water jet cutting, which is more cost-effective for thicker plates.
For thicknesses exceeding 20mm, laser cutting is not recommended due to reduced quality and increased machining needs.
7. Enhance Power for Better Results
More power equals better results when laser cutting aluminum. CO2 lasers mostly fall short in power output compared to fiber lasers.
We recommend choosing a high-powered fiber laser for optimal results. It ensures precision and efficiency when used correctly.
To combat aluminum’s reflectivity, adjust the focusing distance properly. Positioning the focus point towards the far side of the material can help minimise dross formation.
Fiber laser is the superior choice for:
- Burr-free cuts.
- Faster processing times.
- Minimal post-processing requirements.
8. Seek Professionals
For the best results, work with a professional laser cutting service. Experienced providers know how to navigate these challenges. They can deliver high-quality cuts according to your project needs.
So, if you’re looking for an efficient aluminum laser service that expertly tackle these challenges…
Partner With United Metals Laser for Precise & Reliable Aluminum Laser Cutting in Perth
We offer tailored solutions for projects requiring laser and cutting expertise. We make sure using top-notch laser cutters and experienced professionals. Whether it’s intricate designs or large-scale projects, our advanced laser cutter technology ensures flawless results every time.